With over 70 years of history, the client is a professional medical-grade breast pump brand that best meets the clinical requirements of hospitals worldwide. While it may not boast a luxurious appearance like commercial breast pumps, it excels in medical professionalism and is widely used in hospitals and homes in developed markets such as Europe and the United States.
The client's breast pumps, both medical-grade and personal-grade, are designed and manufactured according to the European Medical Device Directive. Their quality and safety standards surpass commercial norms, adhering strictly to medical device regulations. Designed and produced according to medical equipment grades, its breast pumps stand out in terms of materials, craftsmanship, quality, and professionalism compared to ordinary breast pumps, albeit at a higher cost. Nevertheless, the client consistently holds itself to medical standards, providing a professionally reliable breast pump.
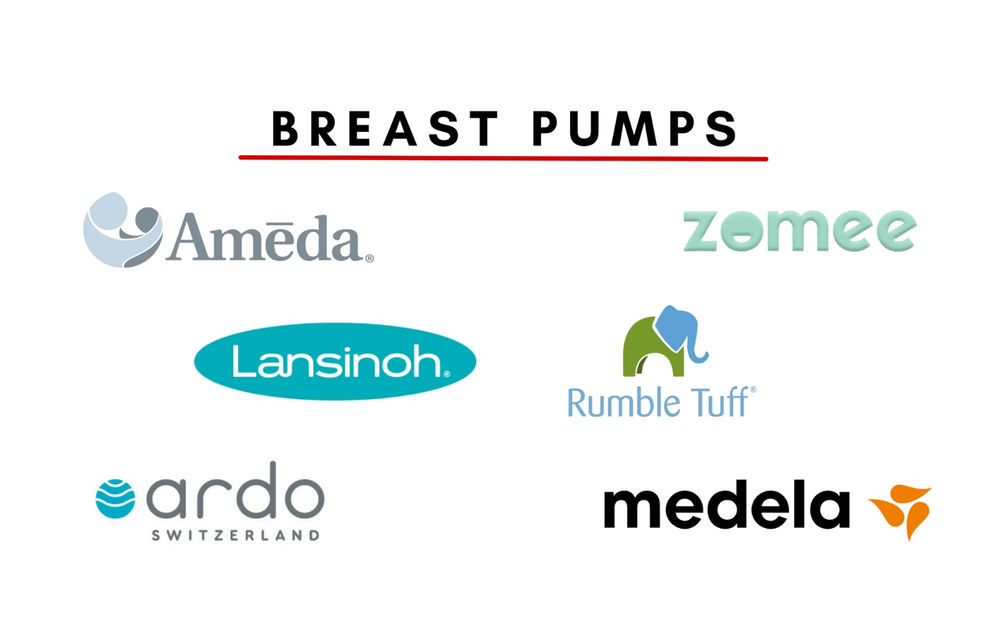
1. The client's current product line significantly lags behind similar products in the market, failing to meet the demands of the younger generation in terms of both appearance and functionality. The business is declining sharply, lacking a competitive edge.
2. The client, as a manufacturer, requires our assistance in obtaining FDA and EU CE certificates. This necessitates the original equipment manufacturer (OEM) to provide a substantial amount of high-standard documentation to meet regulatory requirements.
3. Our founder and the client collaborated on two products: a household breast pump and a high-standard hospital-grade breast pump. The project timeline is urgent, requiring the launch of the household model within one year and the hospital-grade model within a year and a half. The project involves everything from initial design, function confirmation, mold production, testing and certification to formal market release.
4. The client has extremely high requirements for product details, including raw materials, product quality, and precision. For example, the product must achieve utmost precision in shrinkage, requiring coordination across various aspects from mold creation to injection molding. The gap tolerances for plastic parts, for instance, need to be less than 0.02 cm.
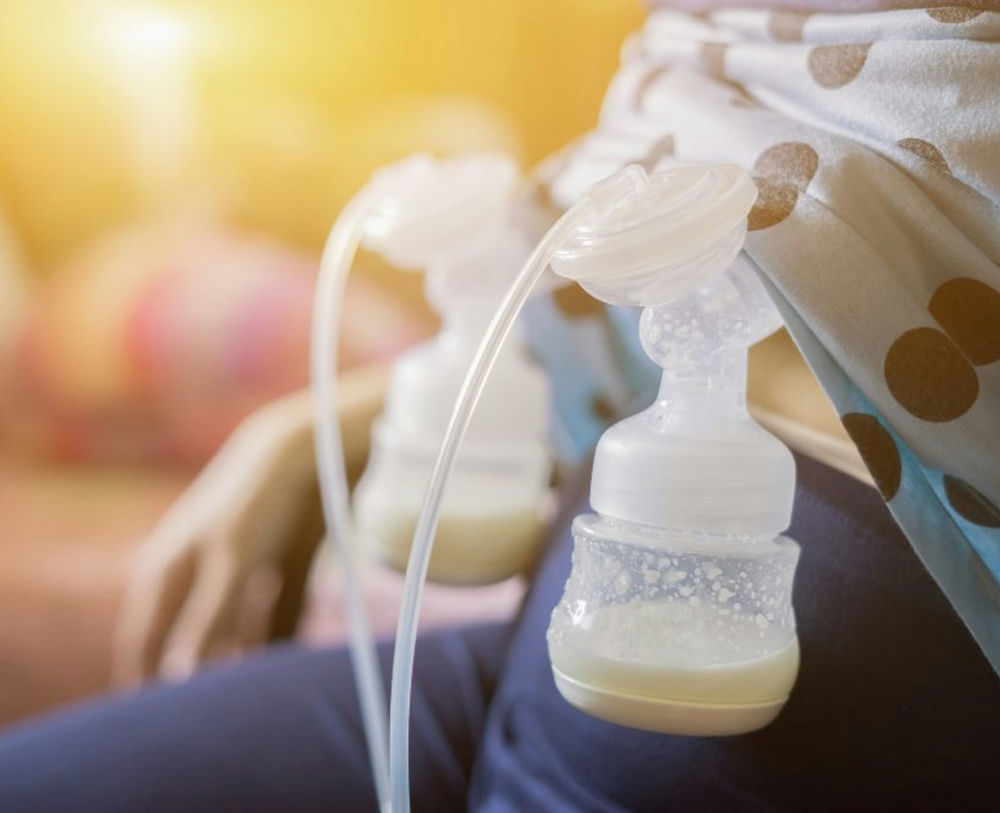
Various challenges encountered during the project's development
1. Two products successfully launched as scheduled.
2. The client obtained FDA and CE certificates on time.
3. Market feedback was enthusiastic, resulting in a business increase of over 86% for the client.
Throughout this remarkable journey, our founder Alison as project manger garnered invaluable project experience. She confronted a myriad of challenges, each met with innovative solutions, delivering exemplary outcomes that exceeded customer expectations.
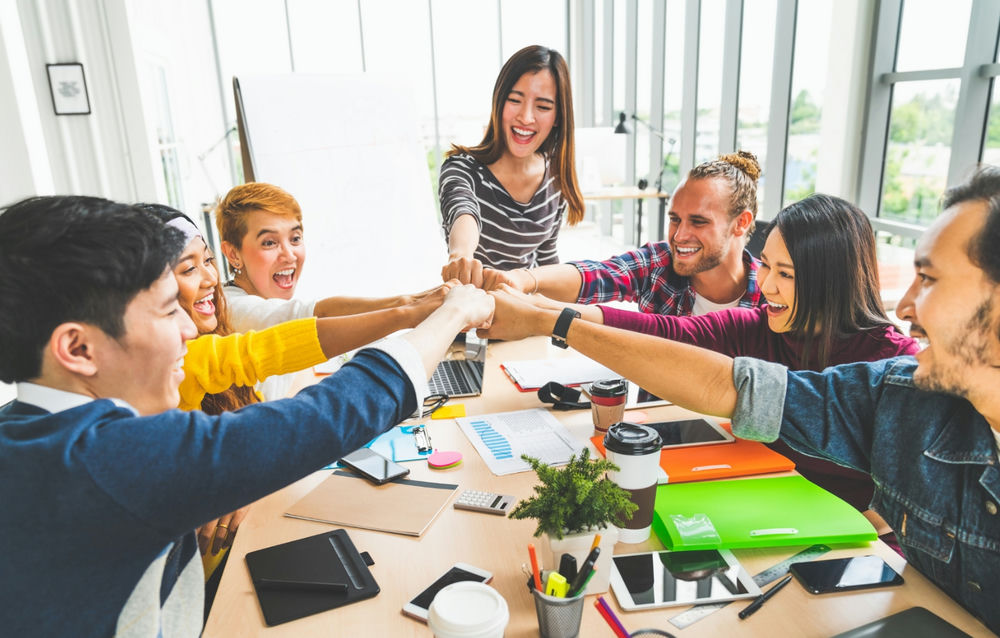
- We Can Do, More Than That.
- We Can Do, More Than That.
- We Can Do, More Than That.
- We Can Do, More Than That.
- We Can Do, More Than That.